Now, let’s consider how you might measure and control product and period cost in a variety of organizations. How would you measure product costs for a merchandiser having a startup? Actually, that’s a fairly easy question. The resources Qarararasha.com spends to acquire store inventory for resale to customers is clearly a product cost. As products are sold, these inventory costs become an expense on the income statement. Well, what about the wages and salaries of Qarararasha’s cashiers, sales associates, and managers? Qarararasha will likely categorize these costs as part of it’s selling and administrative expenses and treat them as a period cost on the income statement.
Related: Selling Online with Ecommerce
Now, consider the same question for a large service business like Ernst & Young, one of the largest certified public accounting firms in the world. What are the products sold by this service firm? Ernst & Young sells the time of it’s tax accountants, auditors, and consultants. The salaries of these professionals represents the cost of it’s product. These costs are reported as the expense, cost of services sold, in the same period in which Ernst & Young the corresponding service revenue.
Related: Market Analysis
Ernst & Young also employs many other people such as clerks, secretaries, and office managers to support the professionals and to administer office needs. The cost of these people are not closely associated with specific consulting jobs. Accordingly, the wages and salaries of these clerks and office managers, along with the cost of office rent, office supplies, and computers are likely treated as period costs and recognized as selling administrative expenses on the income statement in the period in which they are incurred.
Related: How to Make Money with Four P’s of Business Marketing Strategy?
Why is it important for a company to have inventory?
When the demand is uncertain it is hard for a company to predict what the customer is going to want. What the decide to buy now could be different in 3 weeks. So having just the right amount of inventory in stock will let the company have a back up inventory for peaks in demand. — Uncertainty of Supply
DuPont must also employ managers and other support personnel such as engineers and custodians to support the line workers’ efforts to convert basic chemicals into finished products. These are all product costs. Basically, any cost required to get a product manufactured and ready for sale is a product cost. To help management analyze the manufacturing cost of it’s products, product costs are divided into three components. Direct materials, direct labor, and manufacturing overhead.
Many retailers have a fear that the inventory they ordered will not be of the same quality in which they hope, or fast enough to restock the shelves. — Cost of re-ordering
- Raw Materials: Materials purchased and used in production of final product.
- Work-in-process: Goods that are in the process of being manufactured into their final product.
- Finished Goods: Goods that are in their final form and ready to be sold.
Related: Working Capital Management
Remember, product costs are inventoried and move through to the income statement as products or services are sold. Period costs move to the income statement in the period in which those costs are incurred.
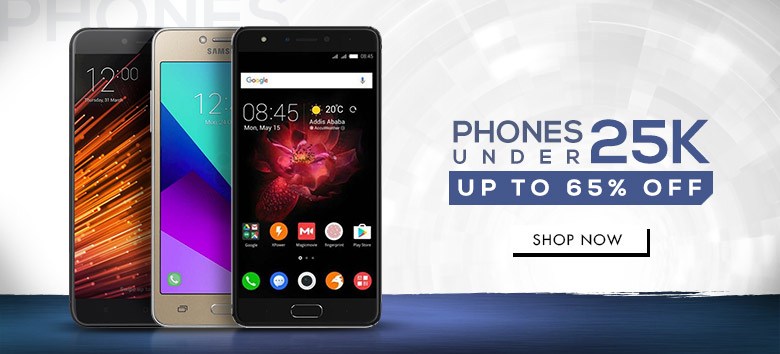